Rolling, Bending & Pressing Work
Rolling, Bending & Pressing Work
A “hydro test” is an approved way to test the structural integrity of a compressed gas container. It is performed by removing the valve, filling the container with water, and then pressuring the container above its operating limit. The expansion of the cylinder is measured, recorded, and analyzed.
The demand for different shapes of bent sheet metal on the market is getting bigger, so in addition to various profiles for boilers, various forms of sheet metal have found a place in the energy industry such as hydroelectric power plants, thermal power plants, wind power, nuclear power plants, etc. For the pipelines of the chemical industry, gas pipelines, high pressure equipment, high-quality reservoir pipes and parts are a necessity. Therefore, it is very important to have the appropriate sheet metal forming equipment, and first of all the heavy duty bending machines specialized for sheet metal.
Roll bending machines with 3 rolls
The machine with 3 rollers usually has two fixed rollers, while the upper vertical roller is positioned accordingly in order to complete the desired bending. By changing the relative position and rotating movement of the working roller, continuous plastic deformation is achieved in order for the workpiece to receive a predetermined shape.
While bending, the work piece is positioned between the lower and upper rollers. After placing the sheet between the rollers, the upper roller is lowered to secure the work piece, and at the same time it has achieved sufficient pressure on the sheet, generating plastic bending. When rotating the roller there is a friction between the sheet metal and the roller, so the sheet moves along its longitudinal direction. At the same time, the upper roller adds pressure to the work piece.
When the roller crosses the lower limit of the upper roller (the roller deformation zone) in one turn and the pressure exceeds the bending limit, plastic deformation occurs and the sheet is folded to its desired dimensions by its entire length. By adjusting the relative position between the lower and upper rolls, the sheet can be folded to a diameter that is not less than the diameter of the upper roller. Here you can see the principle of the symmetrical circular bending machine with 3 rollers:
Rollers 2 and 3 move in the same direction and at the same speed. Because of the friction between the sheet metal and the rollers, the work piece moves in advance. By adjusting the position of the upper roller, the desired bending angle can be achieved. If the work piece does not achieve the proper curvature after the first bending, it can be adjusted and started the process in the opposite direction until the desired shape is achieved.

Machinery
After bending due to the position of the rollers on the work piece inevitably remains a flat part at the ends of the sheet. This flat part is approximately half the length of the gap between the centers of the lower rollers. Although the appearance of a straight part is considered to be a flaw of symmetrical roller with 3 rollers, their simple structure, comfortable use and low price still make them the most wanted model of roll sheet metal bendind machines. In addition, there are methods which we can use in order to easily eliminate this problem. You can find some of them below:
- Pre-bending
– this solution involves bending the edges of the work piece on a press brake before the roll bending process. - Adding a “base” for the work piece during the pre-bending
– this method involves the installation of a “base” together with a workpiece designed for bending and performing the edge pre-bending process on the circular bending machine itself. The application of this method should take into account the possibilities of the circular bending machine and calculate the strength of the applied force on the “base” and the workpiece. - Leaving allowance at the ends
– if you add appropriate allowance at plate ends before the bending, you can, after the bending, cut off those parts into a desired bending shape.
Regarding the asymmetrical models of roll bending machines with 3 rollers, the position of the rollers is better adapted to eliminate the flat edges of the sheet, in which case the lower rollers can also be mounted vertically. Thus, in a model with an asymmetric position of the rollers, the lower rotating roller can be lifted up to the middle of the gap between the two rollers, while the other can be positioned in the appropriate position so that the starting part of the sheet can be folded to form a circle. The flat edge can be eliminated on both sides by turning the rollers in half of the bending process by folding the back of the sheet. Additionally, the work piece can also be turned around after completion of one bending cycle and then the back part will become the front and both flat edges will be eliminated.
Roll bending machines with 4 rolls
In addition to machine tools for roll bending with 3 rollers there are on the market machines for roll bending with 4 rollers. They offer quicker and easier management, but they also have a higher price.
The principle of operation of the roll machine with 4 rolls is similar to the machine with 3 rollers, with the main difference being that the additional roller is used for better input of the material and execution of the process of pre-bending. During bending, the upper and lower rollers are static, the material is firmly positioned between them, and the side rollers move and bend the material. In order to eliminate the flat edges of the material, the lower roller moves upward to hold the material firmly, and the side roller moves and occupies the position for pre-bendind. Unlike a roll bending machine with 3 rollers, where during the pre-bending it is assumed that the material is lowered when entering the machine, in the roll machine with 4 rollers, the material is positioned horizontally, allowing the use of motorized horizontal material holders when inserting materials in certain models. In addition, the input of materials can be carried out on both sides, so the machine can be placed next to the wall and save space.
The advantage of a roll machine with 4 rollers has a unique complete bending process. The machine accepts the material in one stroke, performs the pre-bending and continues to bend the sheet. This system does not require an operator to remove, turn and then straighten the material after pre-bending, as is the case with 3-rollers bending machines. The material remaining in the machine makes the machine with 4 rollers up to 50% more efficient compared to 3-roller models, and allows the material to bend at the desired diameter immediately after pre-bending. The bending of the flat edge starts after bending the material in one direction.
The side rollers are positioned to the left and to the right of the bottom roller, and have their own axes. The independent axis of each roller allows perfect bending. The “rear” side roller (located on the other side of the material insertion) also has a rear end stop function and aligns the material. This feature allows the operator to work without the assistance of other people. Bending in the shape of the coupe is also possible on the machine with 4 rollers. The side rollers can be positioned in the corner for making the coupling and the bottom roller can be lifted to hold and position the material.
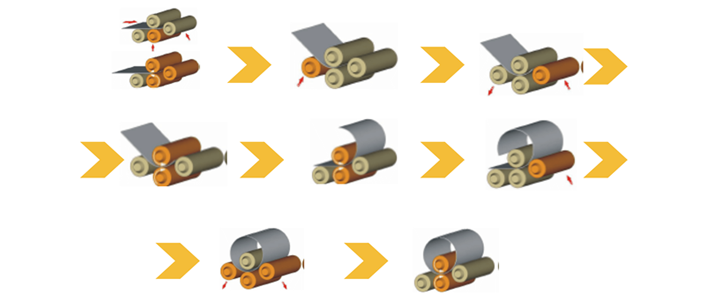
Machines with 4 rollers are faster and easier to operate, and can be managed by a less experienced operator. Ideal for folding materials up to 100mm thickness. However, an experienced operator can perform the same functions on a 3-roller machine, which generally has lower cost and is more commonly found in production facilities.
Roll bending machines with 3 or 4 rollers are the necessary machinery in many industries, and working with them is very simple.